Research on the Potential for Heat Utilization from Renewable Sources Using a High-Speed Microgenerator – MATCHER
The project “Research on the Potential for Heat Utilization from Renewable Sources Using a High-Speed Microgenerator” (MATCHER) is conducted to develop and test a laboratory prototype of a generator with a rotational speed of up to 30,000 RPM, aimed at utilizing heat from renewable sources for electricity production. Successful realization of the project will contribute to the further commercialization of a product that ensures higher energy efficiency in production processes and strengthens collaborative (international) research between the industrial and scientific research sectors.
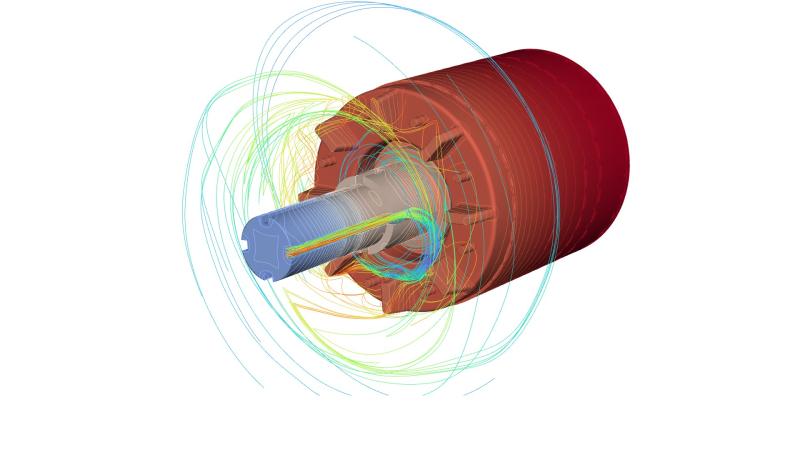
Project Objectives:
- To conduct applied research and develop a prototype (TRL4 level) of a compact high-speed microgenerator to generate green electricity from renewable sources, such as biogas, geothermal energy, concentrated solar power, or waste heat in existing industrial or energy plants.
- To develop, prototype, and laboratory test a high-compactness microgenerator with a power output between 10 and 500 kW and a high rotational speed (8,000 to 30,000 RPM).
- To develop, prototype, and laboratory test a monitoring system suitable for tracking the operation of the microgenerator.
- To research and define the optimal turbine design for two typical cases:
- Microturbine powered by steam
- Microturbine powered by an organic fluid
To design an ORC (Organic Rankine Cycle) plant suitable for electricity production from low-temperature waste heat.
Project Description:
The project aims to conduct applied research and develop a prototype (TRL4 level) of a compact high-speed microgenerator to generate green electricity from renewable sources such as biogas, geothermal energy, concentrated solar power, or waste heat in existing industrial or energy plants.
The potential for energy utilization that a system based on a high-speed microgenerator could harness is substantial. According to some estimates, the EU has significant potential for generating electricity from waste heat (waste-heat-to-power) of around 150 TWh per year (source: “Thermal Energy Harvesting – The Path to Tapping into a Large CO2-free European Power Source”, Knowledge Center on Organic Rankine Cycle Technology, 2022). Additionally, the REPowerEU plan aims to increase biogas production to 35 billion cubic meters by 2030. A micro-aggregator based on a high-speed microgenerator can significantly contribute to utilizing biogas on a micro level (e.g., small farms, smaller agricultural holdings).
This type of microgenerator system will enable the use of energy that has been unprofitable or technically impossible to exploit due to small amounts of heat and lack of space to install reducers and generators. In traditional thermoelectric plants, between the turbine (steam or gas) and the generator, a reducer is necessary to lower the turbine’s high speed to match the generator’s, conditioned by the grid frequency. The widespread use of frequency converters has opened the possibility of directly connecting the turbine to the generator and increasing the operating speed above that determined by the electrical grid frequency, thereby reducing the system’s overall dimensions. A technical solution without the need for a reducer, along with the development of a smaller-sized system with lower cost and maintenance expenses, would allow for installations in places where it was previously impossible due to space constraints.
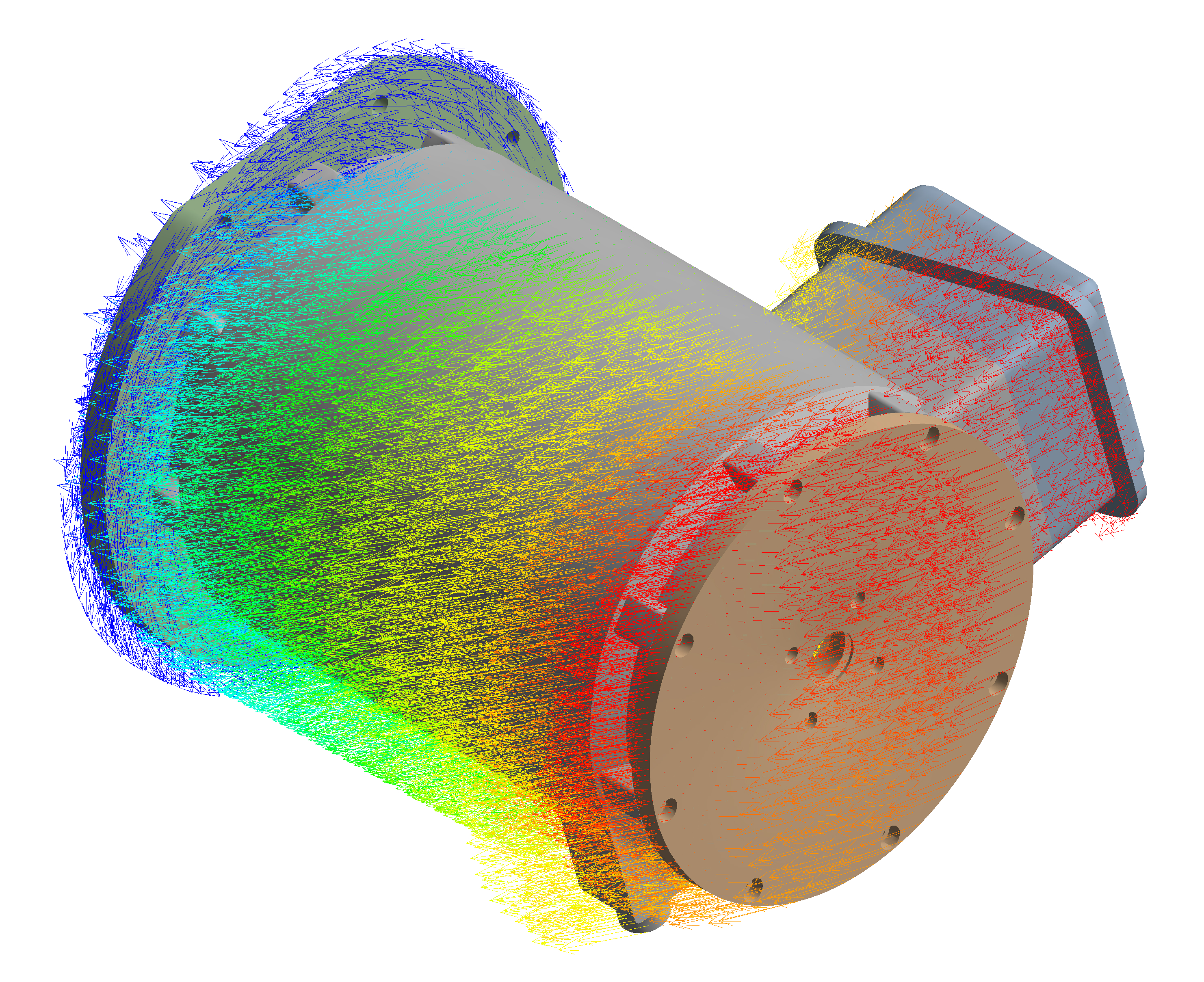
Therefore, the project aims to develop a high-compactness microgenerator with a power output between 10 and 500 kW and a high rotational speed (8,000 to 30,000 RPM), making it easy to integrate into existing industrial plants and enabling profitability in installations with smaller amounts of waste heat.
The research will focus on determining the optimal electromagnetic topology of the microgenerator without the use of rare-earth magnets and other strategic materials, whose future price may increase, and availability could become an issue.
After determining the electromagnetic characteristics, the construction details will be defined. The goal is for the produced prototype to operate for 8,000 hours annually without the need for stopping or maintenance. Efforts will be made to avoid “exotic” construction solutions and components (such as bearings) commonly used in similar machines, which increase the product’s cost, and maintenance requirements, and reduce operational availability.
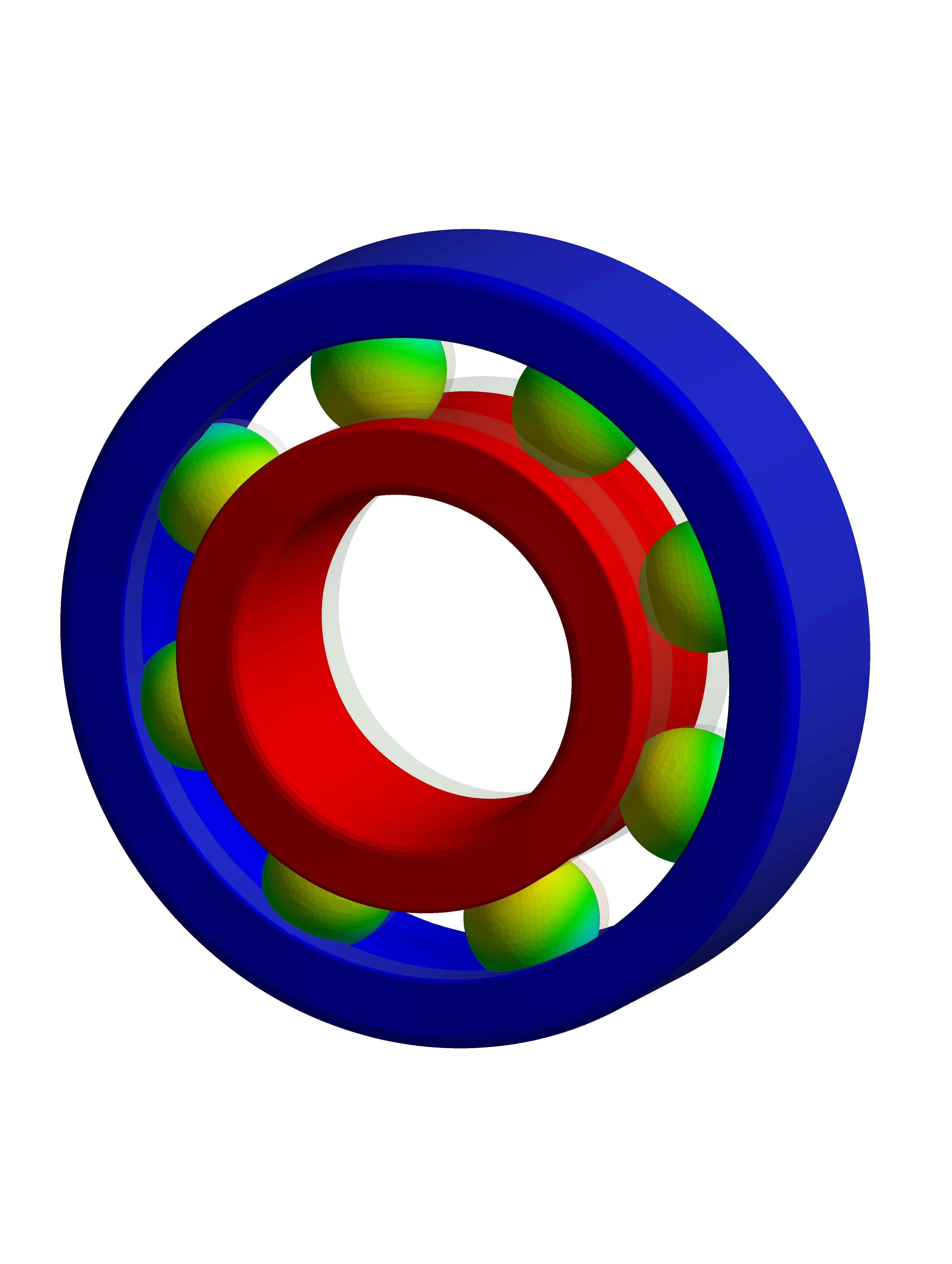
During the design phase, detailed numerical simulations of cooling and mechanical characteristics (strength, fatigue, vibration, and noise) will be conducted to confirm that the machine meets all necessary criteria for continuous operation.
As part of the project, two microgenerator prototypes will be produced and tested in a laboratory using direct load testing, allowing experimental validation of the machine’s designed parameters under various operating conditions.
Since the generator will primarily use heat from renewable sources, the project will include designing the thermal process and turbine. Depending on the temperature level of the source, steam or an organic fluid may be used as the working medium. Therefore, the project will investigate and define the optimal turbine design for two typical cases:
- Microturbine powered by steam
- Microturbine powered by an organic fluid
A comparative analysis of three turbine designs will be performed for each case based on simulation results from computational fluid dynamics (CFD). The goal of these analyses is to select the optimal turbine design for both working media and to determine the specificities that affect the generator’s construction, which is the primary focus of this project.
The results of these analyses will also serve as input data for thermal and rotodynamic analyses of the aggregate and will help determine the optimal method of connecting the turbine to the generator. However, no turbine prototype will be built as part of this project.
To evaluate the heat source’s technically feasible and economically viable temperature level, a design for a typical ORC plant will be developed. This will provide a comprehensive solution for generating electricity from low-temperature waste heat at the project level.
Compatibility between the new high-speed generator and commercially available industrial converters is essential to ensure the solution’s robustness and economic feasibility. This necessitates using established control algorithms, standard voltage levels, a range of operating frequencies, and continuous and short-term current. Compatibility between the generator and converter will be tested in laboratory conditions using prototype machines powered by industrial converters.
Numerous sensors will be integrated into the prototype machines to monitor various operating parameters during laboratory testing. The goal is to validate the calculation results through measurements and ensure operational safety, which is particularly important at high rotational speeds.
As part of the project, the existing monitoring system will be upgraded with a patented safety display concept, adapting it to the needs of monitoring the high-speed microgenerator. This includes developing appropriate system software and upgrading existing Končar electronic modules on the KonFID and KonECS platforms.
This will enable further system digitalization, encompassing: a fast and secure display of the aggregate’s operational state, autonomous operation, remote monitoring, individual and network remote control, intelligent work cycle planning, and intelligent maintenance planning.
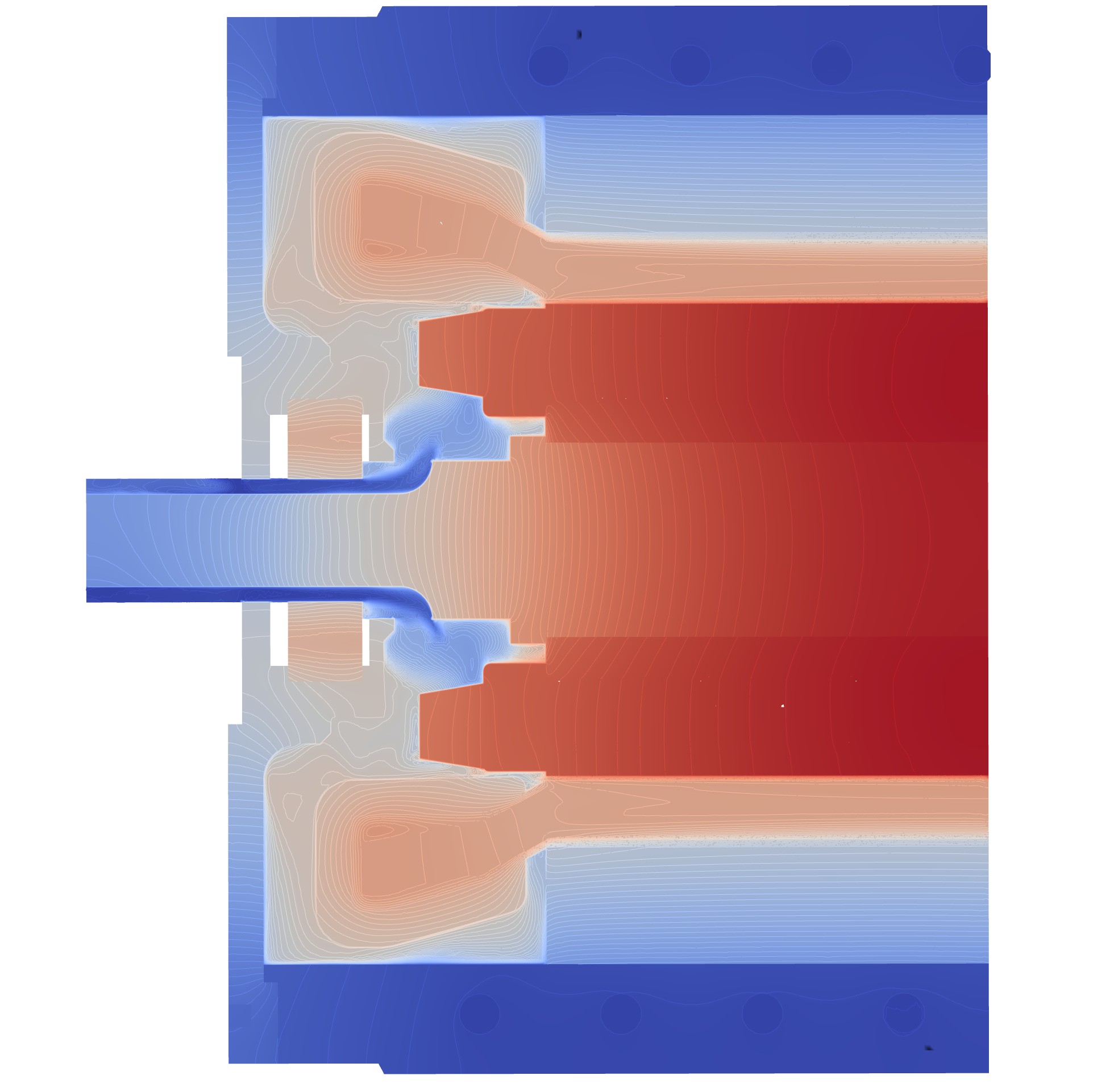
During the project, efforts will be made to achieve the highest possible efficiency for each system component, but primarily ensuring the investment’s economic viability. We believe that only economic feasibility and technically simple solutions will drive the market to invest in generating electricity from renewable sources.
The project will be conducted in collaboration with relevant scientific institutions (Faculty of Electrical Engineering and Computing – FER and Faculty of Mechanical Engineering and Naval Architecture – FSB), providing expertise and support for further development. Collaboration with FER will focus on optimizing the electromagnetic design, while cooperation with FSB will focus on developing the turbine and the appropriate steam cycle.
In conclusion, the development of a high-speed electric microgenerator and steam turbine represents an important step toward energy sustainability, efficiency, and innovation in the industry. This project brings potential benefits for the economy, environment, and society, contributing to achieving future sustainable energy goals.
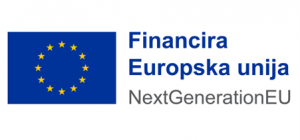