Rotating machinery monitoring systems
Rotating machines are the central and most expensive part of an energy system. Equipping them with monitoring systems facilitates predictive maintenance and effective risk management. Monitoring systems for rotating machines ensure greater equipment availability, enable high operational safety and reduce unplanned outages. They also prolong the service-life of the equipment, offer early fault detection, and improve resource management including time, people, and capital.
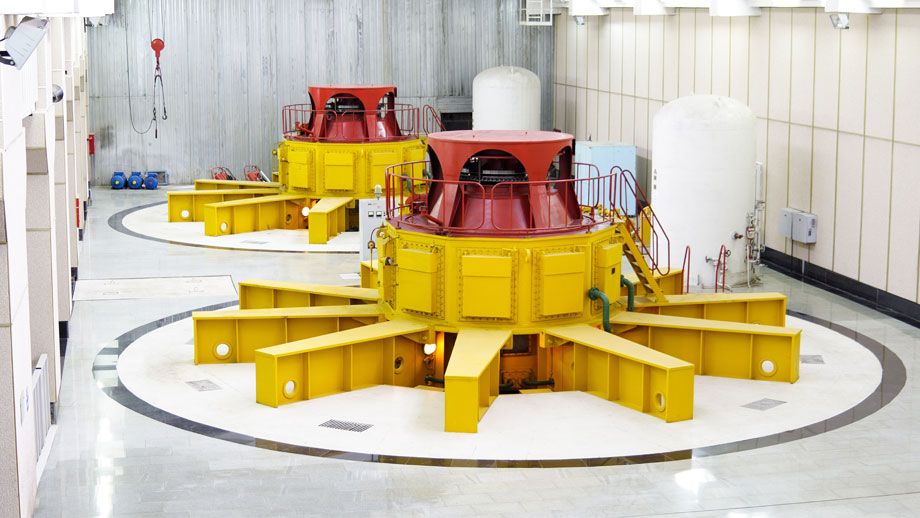
Monitoring systems in power plants come in various forms and functions, each tailored to meet the specific needs of different stakeholders. Despite these variations, their primary objective remains the same: to protect their investment.
When defining and selecting an appropriate rotating machinery monitoring system, it's essential to consider several key questions.
1 Identifying the purpose of the monitoring system
The first step is to set realistic goals. The technical team should thoroughly evaluate critical areas and potential issues that may occur during the operation of key machinery. This includes identifying failure modes, assessing operational risks, and determining the essential functions the monitoring system must perform.
2 Key factors influencing the scope of monitoring
Not all machines require the same monitoring system configuration. To determine the appropriate scope, consider these key questions
- How critical is the generator within the grid?
- What is the current condition of the target equipment, including its age and size?
- What operating conditions is the equipment subjected to?
- How frequently do errors or failures occur?
What potential savings could be realized by investing in a monitoring system?
3 Selecting the appropriate monitoring system
Once you've decided to invest in a predictive maintenance program, consider these critical questions to ensure smooth implementation and continuous operation:
- Will the system be installed on new or existing rotating machinery?
- What types of sensors can be installed – permanently embedded in the generator (magnetic flux, air gap, etc.) or in accessible locations (vibration, speed, etc.)
- Can the system be retrofitted if additional measurements are needed?
- Can the system provide both protection and diagnostic functions?
- How will it integrate with other systems in the plant?
- Will the staff be able to remotely access key information?
These questions will help you navigate the process of selecting the right solution and save you substantial time in later stages. While a robust condition monitoring program cannot entirely eliminate machine failures or production downtime, it can greatly reduce the number of errors that jeopardize plant assets and profitability.